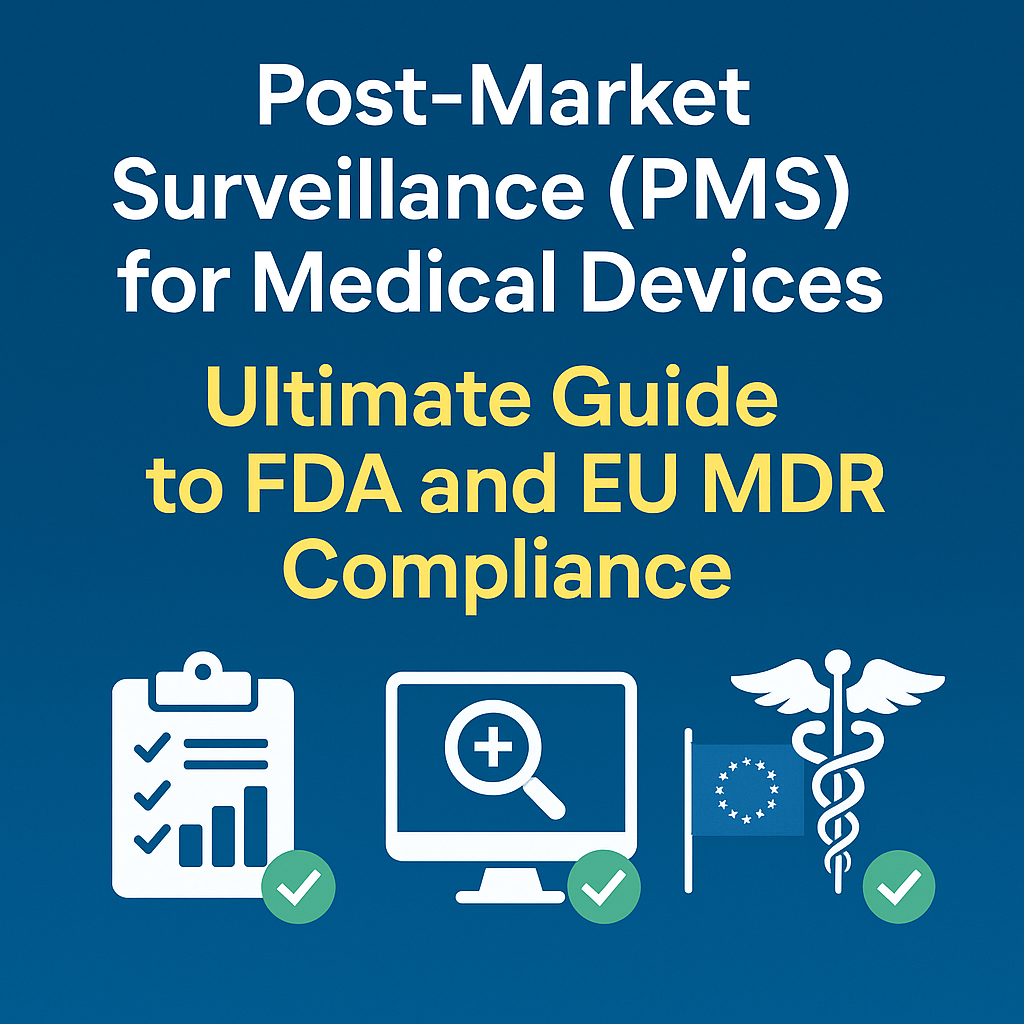
How Mastering Post-Market Surveillance (PMS) Empowers MedTech Businesses
Postmarket Surveillance (PMS) provides your company with the following benefits:
Catch safety and performance issues before they escalate.
✅ Streamline products continually with real-world evidence.
✅ Provide patient safety and company reputation.
✅ Comply with legal needs under the FDA and EU MDR.
✅ Be inspection-ready with clean, auditable systems.
Make PMS your warning system for your QMS, detecting problems in advance and triggering corrective actions.
If your QMS is not yet structured, we recommend beginning with our CAPA Guide and Technical Documentation Guide to prepare for PMS integration.
CAPA Success Made Easy: Your Step-by-Step Guide to FDA and EU MDR Compliance for MedTech Companies
1. What is postmarket surveillance (PMS)? It’s the key to regulatory compliance.
PMS is a structured, ongoing system for monitoring your device’s safety, quality, and performance in the real world after release onto the market.
It goes beyond complaint handling and includes the following:
✅ Structured collection of real-world data.
✅ Analyzing trends and gaining insights into issues.
✅ Channeling insights into your Risk Management File and CAPA system.
✅ Leverage data for product and process optimization.
PMS is legally obligatory under EU MDR and FDA for all medical devices.
2. Step-by-Step Detailed Guide: Building an Effective PMS System
1️⃣ Understand Regulatory Compliance
FDA:
21 CFR Part 820 (QSR) states that PMS interfaces with
Complaint management systems.
The CAPA corrects non-conformances.
The Device Master Records (DHR) facilitate traceability.
Medical Device Reporting (MDR, 21 CFR Part 803): Requires reporting deaths, serious injury, and malfunctions of a particular type to the FDA within specified timeframes.
522 Postmarket Surveillance Studies: The FDA may require postmarket studies for selected high-risk devices.
EU MDR:
Articles 83–86 require:
A PMS plan defining your approach.
PMS reports summarizing findings for Class I devices are required.
The PSUR (Periodic Safety Update Report) is required for Class IIa every two years and for IIb and III every year, and it provides details on benefit-risk evaluation, device usage data, and PMS results.
PMS data feeds into
Clinical Evaluation Reports (CERs).
You use risk management to assess residual risk.
Why it matters:
Knowing these requirements helps you design an audit-ready, legally compliant PMS system that is practically useful for your business.
2️⃣ Draw up a Good PMS Plan
Your PMS plan serves as a roadmap detailing how you will collect, review, and respond to postmarket data.
What it should include:
✅ Device information (intended use, risk class).
✅ Source data you will be using:
Complaint systems.
Adverse event reports.
Literature surveillance.
User questionnaires.
Postmarket clinical follow-up (PMCF) studies.
✅ Analytical methods (trend detection, signal identification).
✅ Responsibilities and roles on your team.
✅ Links to CAPA and risk management procedures.
✅ Reporting obligations (MDR/PSUR deadlines).
Why it matters:
An effective plan confirms that your team knows what data to collect, how to analyze it, and how to report results.
✅ Tip: Format your PMS plan according to ISO 13485:2016 and the EU MDR Annex III.
3️⃣ Establish Systematic Data Collection
PMS success depends on regular, systematic data collection.
Primary sources of data:
✅ Complaints: Device return rates, customer service complaints.
✅ Adverse Events: Hospital statistics, clinician comments, and internal complaints.
✅ Literature Surveillance: Identification of new issues with similar devices.
✅ Registries & Studies: Performance monitoring over the long term.
✅ Service/Maintenance Reports: Service failure trends.
✅ Social Media Monitoring: For patient-facing devices.
Why it matters:
Systematic data collection makes detecting patterns early and not simply reacting to individual complaints possible.
✅ Tip: Use your eQMS to link complaints, service reports, and adverse event reports for easy tracing and tracking.
4️⃣ Analyze Data and Identify Trends
While collecting data is essential, it is equally important to regularly track it to identify patterns.
How to effectively analyze:
✅ Utilize control charts and Pareto analysis to track complaint types.
✅ Track rates of adverse events by product, geography, or lot number.
✅ Look for spikes in specific problems (e.g., sensor failure, battery problems).
✅ Stratify by patient demographics where feasible.
Example:
A current trend of Bluetooth disconnections in a wearable product might indicate a firmware stability issue, necessitating early investigation.
Why it matters:
Early detection allows you to prevent issues from becoming recalls or large-scale failures.
5️⃣ Integrate PMS with Risk Management and CAPA
Your PMS system should integrate well with risk management and CAPA.
✅ Update Risk Management Files (ISO 14971):
Add new risks revealed by PMS data.
Revise risk analysis based on real-world data.
Confirm that risk controls remain effective.
✅ Start CAPA:
Where issues repeat, activate CAPA to:
Assess the root cause.
Take corrective or preventive action.
Confirm effectiveness.
Why it matters:
This closes the quality loop, ensuring PMS results drive actionable improvements.
6️⃣ Meet Reporting Requirements
FDA Requirements:
✅ MDR reporting: Deaths, serious injury, or specific malfunction in 5–30 days.
✅ 522 postmarket study reports were required.
EU MDR Requirements
✅ A postmarket report summarizing activities for Class I devices is required.
✅ PSUR for Class IIa (every two years) and IIb/III (yearly), including:
The report provides updates on the benefit-risk evaluation process.
Data on sales and usage is also available.
The report provides a synopsis of the PMS results and the steps you’ve taken.
Why it matters:
Timely, accurate reporting keeps your business compliant and trustworthy with regulators.
✅ Tip: Maintain a PMS reporting calendar in alignment with your QMS review process.
7️⃣ Continuous Improvement and Management Review
PMS data should inform management review sessions so leadership can observe trends and approve needed improvements.
Apply PMS results to:
Produce design or labeling modifications.
Identify customer or internal groups’ training needs.
Enable product upgrades.
Why it matters:
This makes PMS no longer a regulatory necessity but a strategic business tool, improving your products and processes in a structured manner.
3.⚠️ PMS Pitfalls to Avoid
❌ Collecting data but not reviewing it periodically.
❌ Treating PMS as a reactive complaint system only.
❌ Not linking PMS data to CAPA or risk management updates.
❌ Missing PSUR or MDR reporting deadlines.
❌ Inadequate documentation of PMS activities makes auditing difficult.
4. Best Practices for an Effective PMS
✅ Implement PMS in your QMS proactively, not reactively.
✅ Leverage dashboards to visualize trends.
✅ Define clear thresholds for escalating issues.
✅ Train teams on the value and process of PMS.
✅ Track PMS performance during management reviews
✅ Add PMS findings to your Technical Documentation and Risk Management File.
5. Real-World Example
A healthcare technology firm saw increased reports of adhesive skin irritation in warm and humid regions.
✅ Trend is is identified with PMS trend analysis.
✅ CAPA investigation showed the adhesive formulation was inappropriate for humid environments.
✅ We switched to a hypoallergenic adhesive, updated the Instructions for Use (IFU), and submitted revisions to the Periodic Safety Update Report (PSUR).
The outcome showed an 85% decrease in compliance, an enhancement in patient satisfaction, and an increase in regulator confidence during the audit.
6. Benefits of PMS Mastering
✅ Enhances patient safety and reduces risks.
✅ Strengthens your QMS for FDA and EU audits.
✅ Reduces regulatory risk and potential recalls.
✅ Creates product and process enhancements.
✅ Provides market and regulator confidence.