Introduction: Why Effective CAPA is Your MedTech Growth Catalyst
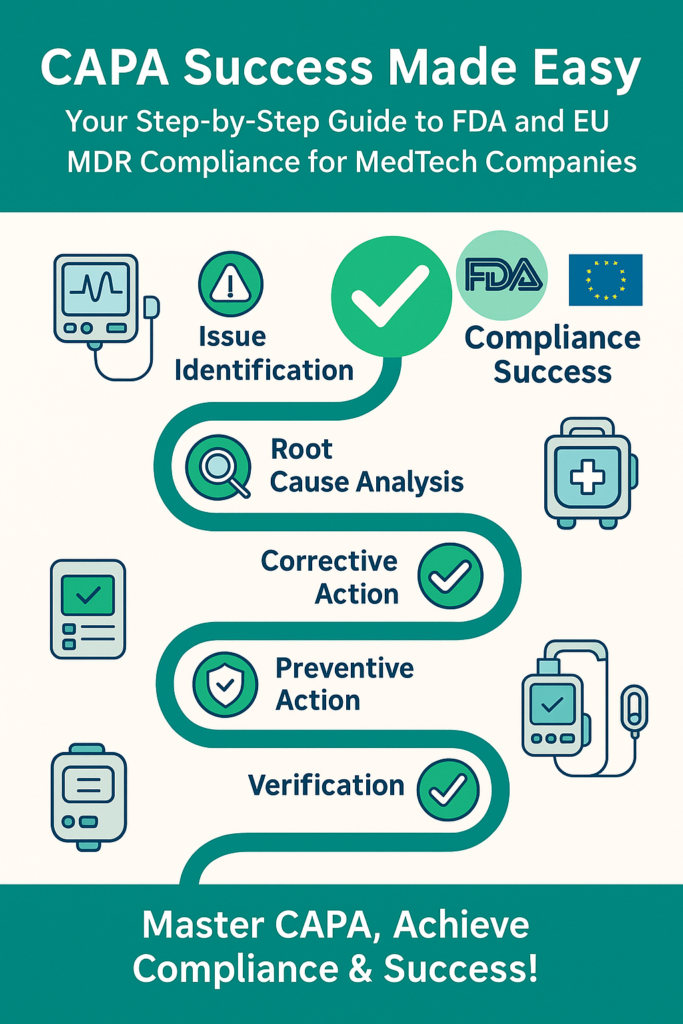
A well-designed CAPA system is a systematic approach to fixing existing issues (corrective actions) and averting future ones (preventive actions) in your medical device products and processes. It is not just regulatory bookkeeping; it is the foundation of operational excellence.
Why a well-designed CAPA system is needed:
Regulatory compliance: Mandated by FDA (21 CFR 820.100), EU MDR (Annex IX and Article 10), and ISO 13485:2016.
Supports patient safety: Retains product integrity and reduces patient risks.
Saves operations costs: Eliminates problems from happening again, reducing recalls, customer complaints, and returns.
Generates reputation: Ensures regulators, customers, investors, and distributors of your dedication to quality.
Facilitates FDA and EU inspections: Enables easy demonstration of proactive quality control so audits go more smoothly.
What is CAPA, exactly?
Corrective Action: Refers to fixing problems that have been identified.
Preventive Action: This is focused on preventing problems from happening in the first place.
A CAPA system:
Step-by-Step Guide: Mastering Your CAPA System
Investigates root causes of issues.
Implements effective remedies.
The process also involves monitoring the effectiveness of the implemented remedies.
Documentation of the process is required.
✅Step 1: Identify and Capture Problems
What is involved:
Active monitoring and documentation of issues from diverse sources.
Sources of issues:
Customer complaints.
Internal/external audits.
Manufacturing defects or non-conformities.
Supplier errors or issues.
Service and maintenance reports.
Trends of Post-Market Surveillance (PMS) (problem or complaint trending).
Doing it the right way:
Use formal procedures (systems or forms) to document every issue on time.
Establish clear issue information: description, product, date, severity, and source.
Example:
Your customer service department has received some battery issues reported with a wearable device. They document this in your CAPA system in real-time, automatically triggering a review.
⚖️ Step 2: Evaluate the Issue and Determine If CAPA is Required
What it involves:
In conclusion, whether or not the issue is severe enough to require CAPA,
Criteria for assessment:
Is the issue systemic or repeated?
Does the issue impact patient safety or device performance?
Is this going to lead to regulatory nonconformity?
Decision-making situation:
Recurring battery failures and patients cutting off from monitoring are systemic risks to patient safety and patently require CAPA.
✅Step 3: Root Cause Analysis (RCA)
Why Root Cause Analysis is required:
Without finding the underlying cause, solutions will be short-lived or unsatisfactory.
Standard RCA tools:
5 Whys: Ask “Why?” until you are left with the underlying cause.
Fishbone Diagram: Charts potential causes into categories (methods, machinery, people, materials, environment).
Fault Tree Analysis (FTA): Depicts potential failure paths in graphical form.
Process Mapping: Identifies precisely where the failure occurred in the process.
RCA example (5 Whys):
Problem: Premature reduction of device battery life.
Why? Firmware is running out too quickly.
Why? Uncontrolled use of power by Bluetooth module.
Why? Firmware problem repeatedly attempting connection.
Why? Firmware not correctly configured during software update.
Root Cause: Firmware update failed proper validation testing.
✅Step 4: Take Corrective Actions
What it involves:
Fixing the root cause to correct the issue.
*** Corrective actions could include:
Revision of SOP or procedure.
Retraining staff.
Repairing or remanufacturing product parts.
Replacement of supplier or raw material.
Revision of software/firmware.
Example
For the battery issue, your fix is a firmware upgrade. You thoroughly document the upgrade process, perform rigorous validation testing, and deploy it in a controlled fashion.
✅Step 5: Define and Implement Preventive Measures
What it is:
Acknowledging potential issues before they are actual issues and putting appropriate preventions in place.
Examples of preventions:
Maintaining regular trending analysis of complaint history.
Conducting regular internal audits to catch minor issues early.
Isolating and fixing quality issues of suppliers.
Example:
Following firmware issue fixes, proactive actions may include quality-tested, automated firmware testing of releases and improving validation processes to avoid such issues in the future.
✅ Step 6: Verify and Validate Effectiveness of Actions
What it involves:
Verify that the solutions implemented effectively resolve the issue without introducing additional issues.
Verification methods:
Tracking complaint level post-implementation.
Inspecting or auditing.
Surveys of internal personnel or user groups.
Data trend and metric evaluation.
Example
After firmware revision, verify by observing customer complaints for three months. When battery complaints significantly decrease, your corrective actions are practical.
✅Step 7: Document and Close CAPA
What it entails:
Complete documentation of the whole CAPA process.
Documentation to include:
Problem description.
The documentation should also include the reasons behind the CAPA decisions.
Documentation of the root cause analysis is conducted.
Corrective and preventive actions are thoroughly documented with timelines.
Evidence of verification and validation is provided.
Signatures from QA or management are required for approval.
Example:
Your CAPA file would include initial complaints, RCA activity (5 Whys), sequential firmware update procedure, validation testing, and complaint data summarized as evidence.
⚠️ Do not Fall Into These CAPA Traps
Avoid identifying the underlying issue, focusing on resolving symptoms rather than the core cause.
Failure to test solutions prior to deployment is a common mistake.
Weak records that cannot stand alone to verify compliance.
Instead of focusing on quality improvement, CAPA is being treated as mere paperwork.
The lack of necessary resources and management support hinders the implementation of CAPA.
✅Best Practices to Ensure CAPA Success
Use formal RCA tools routinely (e.g., 5Whys or fishbone diagrams).
Score CAPAs by risk and severity.
Integrate risk management and PMS systems with CAPA.
Train and inform your staff regularly about the importance of CAPA.
Review CAPA effectiveness in management reviews.
Implement end-to-end traceability in your QMS documents.
🧠Real-World CAPA Success Example
The health-tech startup recognized increasing customer complaints regarding sensor accuracy.
The problem was reported to the CAPA system in a timely fashion.
Root cause analysis revealed temperature exposure during shipping as a cause of calibration drift.
Corrective action improved packaging material and delivery storage requirements.
The preventive actions included conducting supplier audits and performing routine calibration checks.
Customer complaints and sensor accuracy testing confirmed the effectiveness.
Outcome: There was a 90% decrease in complaints, improved compliance, and their FDA inspection was citation-free.
✅Benefits of Mastering CAPA
The benefits of mastering CAPA include enhanced customer satisfaction and improved product quality.
Recalls and complaints result in reduced expenses.
The company is able to undergo inspections by the regulator to ensure compliance with standards.
Continuous improvement in operations is crucial to maintain competitiveness.
The company’s image, as well as the confidence of regulators and customers, has improved.